Essential Pipeline Welding Examination Tips for Top Quality Guarantee
How can one guarantee the quality of these welds that attach the pipeline areas? By comprehending the essential pipe welding inspection ideas, professionals can prevent potential dangers, reduce expensive fixings, and support the integrity of these vital frameworks.
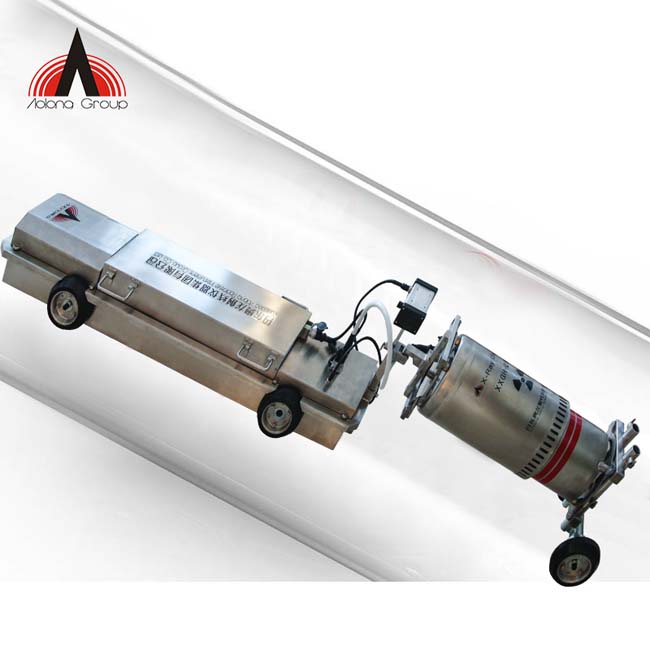
Relevance of Welding Assessment
Welding inspection plays an essential role in making certain the structural honesty and safety of pipe systems. By meticulously taking a look at welds, assessors can determine any kind of defects or flaws that can compromise the stability of the pipe. These evaluations are crucial for avoiding leakages, tears, and various other potentially disastrous failings that could lead to ecological damages, financial losses, and even loss of life.
The relevance of welding inspection can not be overstated, as the high quality of welds straight influences the overall performance and durability of the pipe. Via non-destructive screening methods such as visual evaluation, ultrasonic screening, radiography, and magnetic fragment screening, assessors can detect defects that may not show up to the nude eye. By recognizing and addressing these issues at an early stage, welding assessment assists to make sure that pipes fulfill market requirements and regulative demands.
Eventually, welding assessment is a critical facet of quality control in pipe building and construction, upkeep, and fixing (Pipeline Welding Inspection). By upholding strenuous examination requirements, market professionals can mitigate threats and maintain the security and reliability of pipe systems
Typical Welding Problems
Amongst the obstacles encountered in pipe welding, usual issues can considerably impact the architectural honesty and efficiency of the welded joints. Cracks in the weld can propagate over time, compromising the structural stability of the pipe. Spotting and dealing with these typical flaws via comprehensive evaluation and high quality control procedures are crucial for ensuring the reliability and safety of pipeline welds.
Evaluation Methods for Pipelines
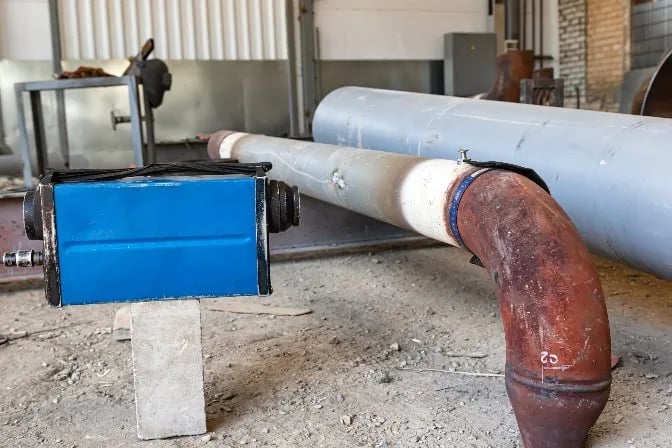

Non-destructive screening (NDT) techniques such as radiographic screening, ultrasonic testing, magnetic bit screening, and liquid penetrant screening are commonly made use of in pipeline welding evaluation. Aesthetic evaluation is additionally important in pipe welding to identify any type of noticeable defects or interruptions. In addition, automated assessment techniques you could try here using innovative technologies like robotics and drones are progressively being used to enhance the effectiveness and precision of pipe inspections.
Ensuring Top Quality Assurance Standards
To maintain rigid top quality guarantee criteria in pipe building and construction, thorough adherence to established industry methods and standards is important. Quality assurance in welding processes requires an extensive method including different stages of pipeline construction. Implementing a robust top quality monitoring system that consists of routine audits and evaluations can even more enhance the overall top quality guarantee requirements in pipeline welding.
Avoiding Costly Repairs
Offered the essential relevance of preserving strict quality guarantee requirements in pipeline construction, an aggressive approach to avoid pricey repair services is vital. By implementing thorough examination procedures throughout the welding process, prospective issues can be recognized and remedied at an early stage, inevitably conserving both money and time. One vital aspect of protecting against expensive repairs is making certain that welders are correctly educated and accredited, as this dramatically minimizes the likelihood of malfunctioning welds that may cause future failings. Furthermore, making use of sophisticated examination techniques best site such as non-destructive screening can help find any flaws or incongruities in the welds before they intensify right into major issues. Normal maintenance checks and tracking of ecological elements that might influence the integrity of the pipeline are also crucial in stopping pricey repairs. By buying preventative procedures and focusing on quality assurance at every phase of the pipe welding procedure, companies can reduce the danger of pricey fixings and ensure the long-lasting dependability of their framework.
Conclusion
To conclude, adherence to correct welding like it examination strategies is necessary for guaranteeing the quality and honesty of pipes. By determining common welding issues and carrying out complete evaluation processes, pricey repair work can be prevented, and quality control standards can be fulfilled - Pipeline Welding Inspection. It is important for pipeline welders to focus on evaluation treatments to preserve the safety and integrity of the infrastructure they are working with
The significance of welding inspection can not be overemphasized, as the quality of welds straight impacts the general performance and durability of the pipeline. Non-destructive screening (NDT) techniques such as radiographic testing, ultrasonic screening, magnetic bit screening, and liquid penetrant screening are commonly used in pipe welding evaluation. Aesthetic evaluation is additionally important in pipe welding to identify any type of noticeable defects or interruptions. Additionally, automatic examination techniques using innovative technologies like drones and robotics are increasingly being employed to improve the performance and accuracy of pipe examinations.In conclusion, adherence to correct welding examination methods is vital for guaranteeing the top quality and integrity of pipelines.