Porosity in Welding: Identifying Common Issues and Implementing Best Practices for Prevention
Porosity in welding is a pervasive problem that typically goes unnoticed up until it triggers considerable troubles with the honesty of welds. This usual issue can compromise the strength and sturdiness of welded structures, posturing security threats and bring about pricey rework. By recognizing the origin creates of porosity and applying reliable avoidance approaches, welders can dramatically boost the high quality and dependability of their welds. In this conversation, we will certainly check out the essential elements contributing to porosity formation, examine its destructive results on weld efficiency, and go over the most effective practices that can be adopted to lessen porosity incident in welding procedures.
Typical Sources Of Porosity

Making use of filthy or wet filler products can present pollutants into the weld, contributing to porosity problems. To mitigate these usual reasons of porosity, thorough cleansing of base steels, proper securing gas selection, and adherence to ideal welding criteria are important techniques in achieving premium, porosity-free welds.
Influence of Porosity on Weld Quality

The presence of porosity in welding can considerably jeopardize the structural stability and mechanical residential properties of bonded joints. Porosity produces spaces within the weld metal, weakening its total toughness and load-bearing ability.
Welds with high porosity degrees tend to show lower influence strength and lowered capability to flaw plastically before fracturing. Porosity can restrain the weld's capability to properly transfer pressures, leading to premature weld failure and possible security threats in vital frameworks.
Finest Practices for Porosity Avoidance
To boost the architectural integrity and high quality of bonded joints, what details procedures can be carried out to lessen the incident of porosity throughout the welding procedure? Using the appropriate welding technique for the specific product being welded, such as readjusting the welding angle and weapon position, can better stop porosity. Routine evaluation of welds and immediate removal of any kind of problems determined throughout the welding procedure are necessary practices to protect against porosity and create top quality welds.
Value of Correct Welding Strategies
Executing correct welding strategies is vital in making certain the structural integrity and high quality of bonded joints, building upon the foundation of effective porosity prevention measures. Excessive heat can lead to raised porosity due to the entrapment of gases in the weld pool. Additionally, making use of the ideal welding specifications, such as voltage, present, and travel speed, is important for accomplishing audio welds with very little porosity.
Additionally, the selection of welding process, whether it be MIG, TIG, or stick welding, need to align with the certain requirements read of the project to make sure optimal outcomes. Correct cleansing and preparation of the base metal, in addition to picking the right filler material, are additionally necessary components of skillful welding methods. By sticking to these finest methods, welders can decrease the risk of porosity development and generate top notch, structurally sound welds.
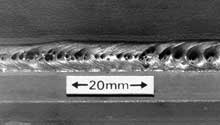
Examining and High Quality Control Measures
Quality control actions play a crucial duty in verifying the integrity and dependability of bonded joints. Checking treatments are necessary to spot and avoid porosity in welding, making sure why not try this out the strength and toughness of the end product. Non-destructive screening techniques such as ultrasonic screening, radiographic screening, and aesthetic examination are commonly employed to identify potential defects like porosity. These techniques permit the assessment of weld high quality without compromising the integrity of the joint. What is Porosity.
Post-weld examinations, on the other hand, evaluate the last weld content for any kind of defects, including porosity, and validate that it meets defined criteria. Implementing a detailed top quality control plan that includes thorough screening procedures and examinations is extremely important to lowering porosity issues and making certain the overall quality of welded joints.
Conclusion
Finally, porosity in welding can be an usual issue that impacts the high quality of welds. By identifying the common causes of porosity and carrying out best practices for avoidance, such as proper welding techniques and testing procedures, welders can make sure excellent quality and trusted welds. It is vital to prioritize avoidance methods to lessen the occurrence of porosity and maintain the stability of bonded frameworks.